Car makers switch to smaller and safer robots working alongside humans for greater flexibility
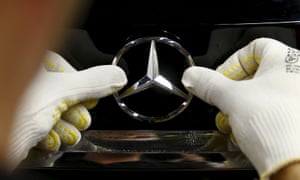
Bucking modern manufacturing trends, Mercedes-Benz has been forced to trade in some of its assembly line robots for more capable humans.
The robots cannot handle the pace of change and the complexity of the key customisation options available for the company’s S-Class saloon at the 101-year-old Sindelfingen plant, which produces 400, 000 vehicles a year from 1,500 tons of steel a day.
The dizzying number of options for the cars – from heated or cooled cup holders, various wheels, carbon-fibre trims and decals, and even four types of caps for tire valves – demand adaptability and flexibility, two traits where humans currently outperform robots.
Markus Schaefer, Mercedes-Benz’ head of production told Bloomberg: “Robots can’t deal with the degree of individualisation and the many variants that we have today. We’re saving money and safeguarding our future by employing more people.”
The automotive industry is the largest user of industrial robots, according to the International Federation of Robotics (IFR), accounting for nearly 100,000 units shipped in 2014. The total number of industrial robots in operation worldwide was 1.5m in 2014, while the IFR expects 1.3m more to come online in the next two years.
But with increasing competition for consumers’ money in the luxury market, customisation has become key. At the same time, the rate at which models, technology and options change has increased as car makers have diversified their offerings.
Skilled humans can change a production line in a weekend, where robots take weeks to reprogram and realign.
‘People taking a bigger part’
Schaefer said: “We’re moving away from trying to maximise automation with people taking a bigger part in industrial processes again. We need to be flexible. The variety is too much to take on for the machines. They can’t work with all the different options and keep pace with changes.”
Schaefer seeks to reduce the time taken to produce a car from 2005’s standard of 61 hours to just 30. To do so, Mercedes is shifting to what it calls “robot farming” – equipping workers with an array of smaller, lighter machines. Traditionally robots would operate behind safety fences in isolation from human workers.
The change will mean smaller, more flexible systems that work side-by-side with humans will replace some of the large traditional robotic machines, including in the production of the new Mercedes E-Class. A human or a lightweight machine will replace two fixed robots for the alignment of the car’s new heads-up display, which projects speed and directions on to the windshield.
Mercedes, the second-largest manufacturer of luxury cars, is not alone in this shift to more flexible systems. German competitors BMW and Audi are also testing robots equipped with sensors and intelligence that are safe enough to work alongside humans.
Even in Japan, the world’s leaders in industrial robotics, Toyota has begun similar processes, replacing robots with humans to counter-intuitively increase efficiency and reduce waste.
The key is to maintain the qualities of robotics, consistency and reliability, while gaining an edge to be quicker to change as the automotive industry adapts to new technology. Traditional car manufacturers are increasingly coming under pressure from companies such as Tesla, born of the fast-paced technology industry.
Where a smartphone can be conceived, developed and put on sale within 18 months, a traditional car typically takes seven years to hit production. At the same time models have proliferated, customisation has become the key and mass-production simply isn’t good enough.
To keep pace Mercedes will produce an additional 30 models by the end of the decade, with 10 new styles and more and more options from car fragrances to custom lighting.
[Source:- Gurdian]